The Scope of Work Member community is a space for learning together and tackling the vexing challenges inherent in making physical things. The #general-questions channel is among the most active on our Slack, fielding queries – and supplying answers – about sourcing, prototyping, and material choices. As part of our commitment to supporting Members in their work, we recently launched community AMAs, in which interesting and accomplished Members share wisdom and expertise from their work experience.
Our first AMA was with designer and product coach Tom Gerhardt. In 2010, after the stratospheric success of their first product on Kickstarter, he co-founded the lifestyle brand Studio Neat with Dan Provost. Since then, Tom has designed over 30 products, from Apple accessories to a line of cocktail tools and, most recently, pens and notebooks. He has taught product development at NYU and hosts a podcast about product design and running an indie business. Today, he runs a product coaching practice that helps translate ideas into new consumer products and services. Tom spent more than two hours graciously sharing his perspective on product and business development, which we’ve condensed and lightly edited.
Eric Andersson: To what extent do you do your own design-for-manufacturing/assembly optimizations in your work, versus enabling your manufacturers to make and suggest those optimizations?
Tom Gerhardt: We basically do it all. Much of that work is at the very beginning when we are trying to figure out the constraints of a process or finish. I usually talk to the manufacturer (or just some random manufacturer in the space) and find out what the design constraints are. Sometimes I send a sketch or render to ask if it’s hard or crazy. DFM is from the very beginning. Because we have to do everything, we can’t just do some fancy ID-style sketch in a notebook and send it to the engineering team.
We make aesthetic and engineering decisions at the same time.
Come to think of it, I bet this has a lot to do with why the objects we design seem simple and honest. It’s all very functional/practical. One thing we’ve been conscious of as we grow a team is we want to stay very close to all the processes. I WANT to know all the engineering constraints. There is a very sweet satisfaction in designing a part that is efficient to produce. So much so that often I fantasize about producing parts in-house, but the downside of that is you are locked into a lot of overhead.
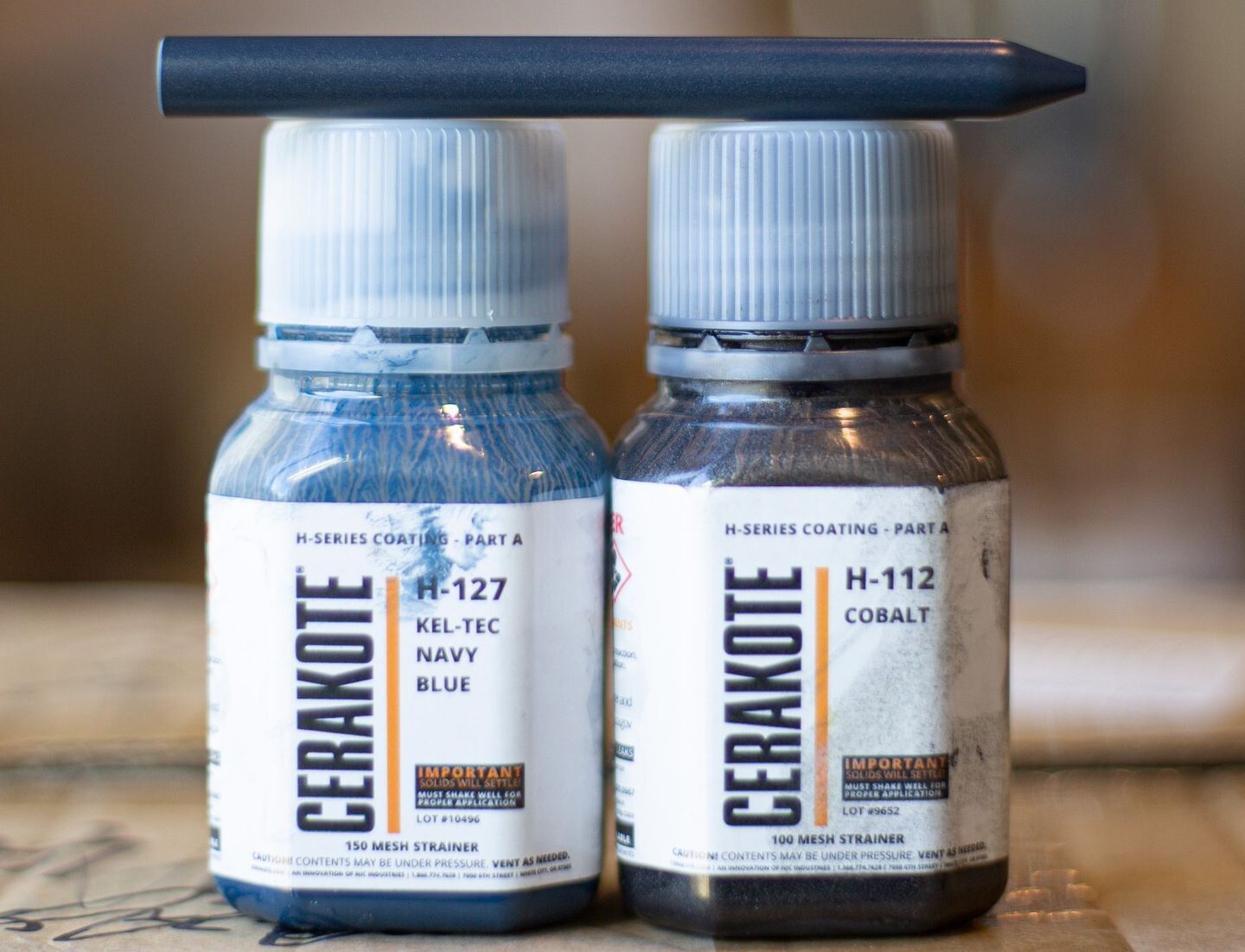
George Cave: Your products place a big focus on the materials and finishes used, so I assume you spend a long time sourcing and researching materials and suppliers. Do you design the product first or the material first? i.e. - how often do you come across new materials or finishes (e.g. some of the Mark One limited editions spring to mind here) and work backward thinking "I love this, I wonder how I can make use of it"?
Read the full story
The rest of this post is for paid members only. Sign up now to read the full post — and all of Scope of Work’s other paid posts.
Sign up now