The Coanda effect and why we transform nuclear waste into borosilicate glass.
Every week, after the flagship Monday issue of this newsletter is sent out, emails from readers like you start trickling in. We read every single one, and the experience is enlightening; you folks invariably draw fascinating and delightful connections from the things we share. Today, we bring you just such a connection - a particularly fascinating conversation with a reader of this newsletter.
In 2021-07-12, Spencer wrote about Plateau-Rayleigh instability - the phenomenon in which streams of liquid tend to break up into discontinuous droplets - and Tom Kocialski wrote back to say that it reminded him of the Coanda effect - the tendency of a fluid jet to stay attached to a convex surface. As Tom wrote, “the Coanda effect can be encountered when you pour your tea slowly out of a teapot and observe that it often tends to flow partly downwards over the lip of the spout instead of directly out of its mouth.”
He also mentioned the project that introduced the Coanda effect into his work: engineering a melter to vitrify (to transform into glass) high-level nuclear waste. We just had to learn more, and since then Spencer and I have traded a series of emails with Tom - about his career, his work, and about what happens to radioactive material when humans are done playing with it. And so, our guest this week is Tom Kocialski PE: a USAF veteran and retired engineering manager who worked primarily in the nuclear waste business. His career brought him to many sites across the US, including the Fast Flux Test Facility, the Waste Isolation Pilot Plant (WIPP), the West Valley Demonstration Project (WVDP), and the Pit Disassembly and Conversion Facility (PDCF). At West Valley, Tom ran the startup, engineering operations support, and shutdown of the Vitrification Facility. Today he does volunteer work in his community, spends time with his family, and answers the questions of nosy nerds. What follows are lightly edited highlights from our conversations with him.
How is nuclear waste classified, and what does that mean for storage and disposal?
The classification of radioactive waste is a fairly complex topic. The US Waste Classification system is different than the International Atomic Energy Agency (IAEA) system; here’s a fine slide show that simplifies the classification schemes.
Low-level waste (LLW) | High-level waste (HLW) | Transuranic waste (TRU) | |
---|---|---|---|
Common examples | Contaminated garments, office supplies, construction materials | Reprocessed spent nuclear fuel, and LOTS of waste material from the defense industry | Garments, tools, and other gear that has been contaminated with elements heavier than uranium |
Characteristics | Can range from just above background level to highly radioactive | HLW is defined by origin, not activity, and is highly radioactive | Highly alpha-emitting |
Disposal options | Near-surface disposal at ground level, or in caverns below ground level (at depths of tens of metres) | Deep geological disposal (at depths between 250 m and 1000 m for mined repositories, or 2000 m to 5000 m for boreholes) | Deep geological disposal (at depths between 250 m and 1000 m for mined repositories, or 2000 m to 5000 m for boreholes) |
Chart adapted from the United States Nuclear Regulatory Commission.
In brief, Low-Level Waste (LLW) is classified as A, B, or C, depending on the concentration of radionuclides present in the waste. The guidelines for storage are more stringent as you go from class A to class C. LLW can be disposed of in near-surface facilities rather than in a geologic repository. High-Level Waste (HLW) is generally either reprocessed spent nuclear fuel (SNF) from a reactor, the liquid residue from fuel reprocessing, or defense-related waste. In the US, most of this residue was generated by reprocessing fuel from government reactors. SNF and HLW are highly radioactive and require significant shielding to protect humans from immediate harm and require geologic disposal.
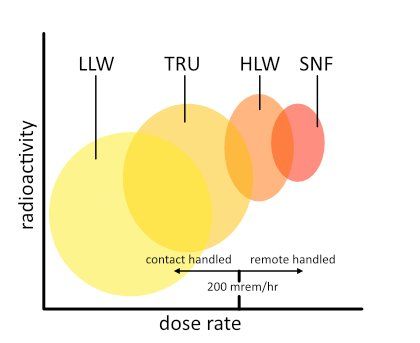
The US system includes a category for transuranic radioactive waste (TRU), waste that contains man-made elements heavier than uranium on the periodic table. Importantly, it looks like LLW but must be disposed of in [underground] geologic repositories. Most transuranic wastes are essentially alpha-particle emitters, whose radiation can be shielded by something as thin as a sheet of paper. However, if it enters your body this radiation is known to cause cancer. Pu-239, which is included in transuranic waste, has a half-life of 24,000 years. It is produced during nuclear fuel assembly, nuclear weapons research and production, and during the reprocessing of spent nuclear fuel.
There is a lot of TRU waste because the actual contamination is not separated from the contaminated objects. While I have never peeked in any of the barrels of TRU, pictures show them to be full of things like contaminated labware, tools, protective clothing, booties, and so on. One estimate is that eventually almost 20,000 shipments of TRU waste - each roughly a tractor trailer with multiple containers - will be sent to WIPP for tens of thousands of years of isolation!
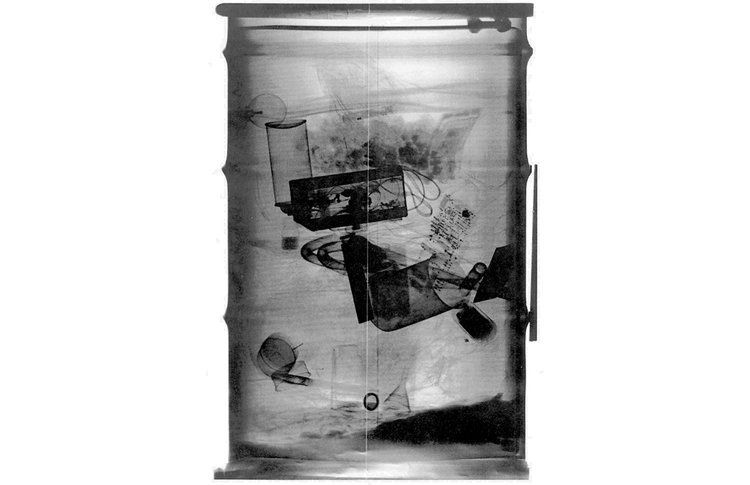
Can you tell us more about the Vit Facility - what actually takes place there?
In 1993, I transferred to the West Valley Demonstration Project (WVDP) in Western NY, and was assigned as the startup and commissioning manager for the High-Level Waste Vitrification Facility - colloquially referred to as the Vit Facility. The WVDP site was originally the location of a nuclear fuel reprocessing facility, commercially operated but owned by the New York State Research and Development Authority. This facility was designed to combine the HLW with glass-forming chemicals, creating a mixture that was introduced to a high-temperature melter and formed into a molten glass compound. The glass was poured into stainless steel canisters which were subsequently sealed and put into temporary storage on site.
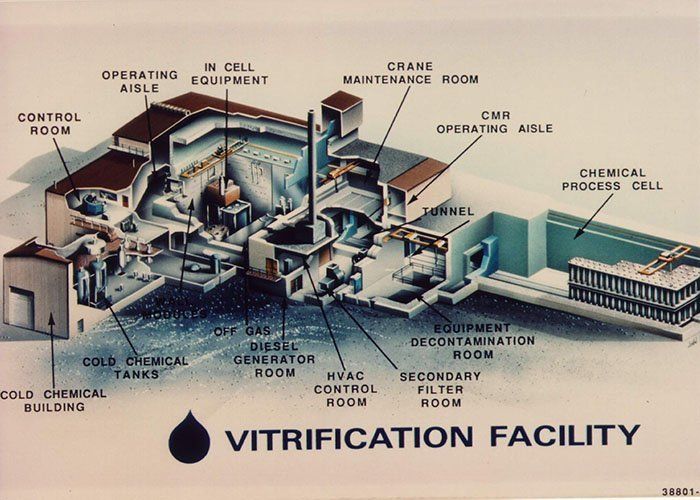
What's the rationale for doing this in the first place - what's the benefit of turning nuclear waste into glass?
In the glass matrix, the HLW is highly impervious to separation. If a geological repository were to be flooded and the stainless steel canisters breached, the water would be incapable of leaching out the HLW from the glass matrix.
The liquid High-Level Waste (HLW) at West Valley consisted mainly of cesium and strontium leftover from nuclear fuel reprocessing operations in the 1960s. The waste was stored as liquid and sludge in an underground tank system or tank farm. These tank farms are not designed to be permanent storage facilities, so a process to convert the liquid HLW into a stable solid form suitable for permanent storage was needed - hence the design, construction, testing, and operation of the Vit facility.
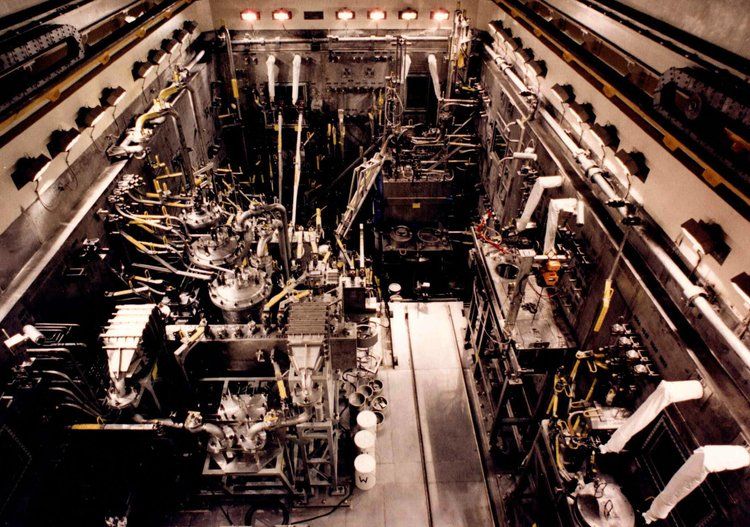
The Vit Facility was a large, shielded cell with several key components: a concentrator tank, a feed/hold tank, the vitrification melter, a welding station to seal the top of waste canisters, and a device to transfer the filled canisters to an interim storage facility. Liquid HLW was pumped from the tank farm to the concentrator tank, and a batch of glass-forming chemicals was pumped into the concentrator tank where excess water was evaporated. When the resulting slurry was ready, it was transferred from to the feed/hold tank so another batch could be prepared.
While preparing the next batch in the concentrator, the slurry in the feed/hold tank was slowly transferred to the melter, where molten glass was being heated by electric currents. The slurry was transferred to the top of the molten glass, where it slowly blended with the glass already in the melter. Stainless steel canisters were rotated into position beneath a pour spout of the melter, and the molten glass was airlifted - an interesting process in itself - into a canister.
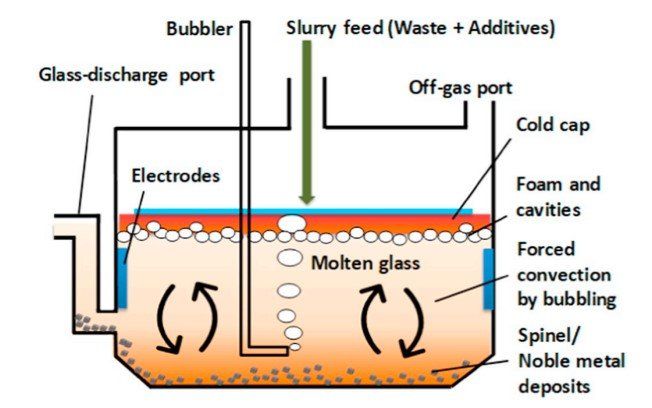
By bubbling air into the overflow passage, the mixture of glass and air was less dense than the glass below it, so the heavier glass pushed the glass/air mixture further up the channel where it was able to overflow via the spout and drip into the canister. It was a slow drip of very viscous glass, so the Coanda effect caused it to adhere to the lip of the spout and flow a bit before it came loose from the exterior of the spout and passed into the canister - that’s how this whole thread started!
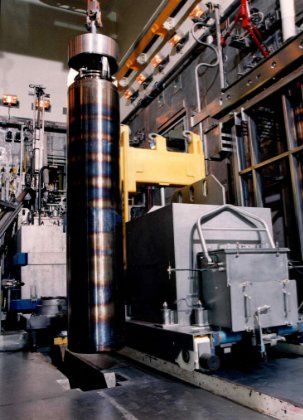
When the canister was full, it was brought to a station where a lid was remotely welded to its top, sealing in the glass which was slowly solidifying. Each canister held about 2,000 kilograms of glass. The sealed canister was then transferred to an adjacent interim storage facility.

Can you give us an overview of the operations? What happened once all the waste had been processed?
The vitrification process began in June 1996 and there were two distinct phases to the operations of the facility. The first phase of the program vitrified the majority of the HLW from the tank farm. The second phase was associated with a lot of cleaning and flushing of facilities and process equipment to ensure that the vast majority of any residual HLW was duly vitrified. Rather than test my feeble memory, I’ll copy the summary from a report prepared for a 2003 conference:
The WVDP is the first HLW immobilization project brought to completion in the U.S. Radioactive operations conducted in two phases over six years resulted in the immobilization of about 24 million curies of radioactive material into 275 cans of HLW glass. Continuous melter operation and 71% plant availability (86% in the first year) resulted in the production of 211 canisters made from 54 feed batches that were filled to 90%. The second phase of radioactive operations resulted in the production of 64 canisters from 15 batches of HLW feed material prepared from cleaning and flushing of the HLW tanks, cell walls, sumps, and slurry transfer lines. After the last canister of HLW was produced using the Vit System, the melter was shutdown [sic] and emptied using two evacuated canisters. These operations were completed in September 2002, marking the end of six years of successful Vit System operation and solidification of HLW at the WVDP.
At the end of operations, there was an insufficient mass of glass to airlift out so special evacuated canisters were designed to suck the molten glass out of the melter by a port opening in the top. That was also an amazing, one-time, awesome event I’ll remember forever.
The evacuated canisters had a snout that was plugged with a metal compound, designed to melt after it was inserted into the molten glass. A vacuum of approximately one atmosphere was applied to the canister, and after the plug melted, the glass was siphoned out of the melter cavity. The engineers got the idea while playing around with one of those bendable soda straws at lunch one day - go figure. Those are the creative thinkers that I enjoyed working with. Yes, we tested it, but it was a really nerve wracking experience to be there in person to watch it work. Our small team stood at one of the shielded windows, peering into the Vit cell as the canister’s snout was lowered into the melter.
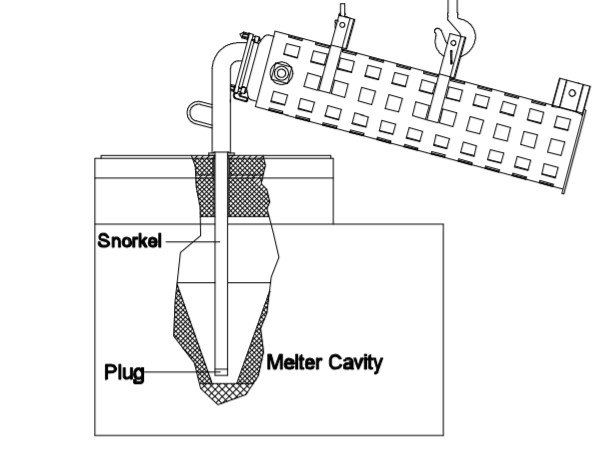
The crane holding the canister had a load cell to measure the weight of the canister and its contents. We were expecting to see the weight increase as the glass was drawn up into the canister by the vacuum inside it. Yes, we saw the weight change, but we also saw the canister and snout start to glow red hot as the glass was sucked in. I guess we all should have expected it, but it was an awesome sight to see this massive thing start to glow cherry red! Of course, we were surrounded by our local corporate and DOE staff, who were, shall I say, duly impressed. It was quite a show!
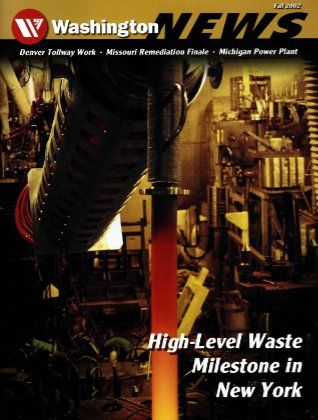
How did we feel? Relieved, excited, thrilled that everything worked as planned. Ready to get on with whatever came next, expecting that it would be a lot less exciting than what we just witnessed.
The vitrified HLW from West Valley was supposed to be stored at Yucca Mountain, but that project hasn't moved forward. What happened with the Yucca Mountain repository?
The Yucca Mountain Repository was to store spent nuclear fuel from reactors as well as HLW from government facilities - but it was met with political opposition from state, local, and tribal leaders. The story is as much about politics as it is about science, and a laundry list of concerns has kept the project from making any significant progress. The Government Accountability Office was prodded to determine why the Obama administration shut it down and determined that it was done for political rather than scientific reasons.
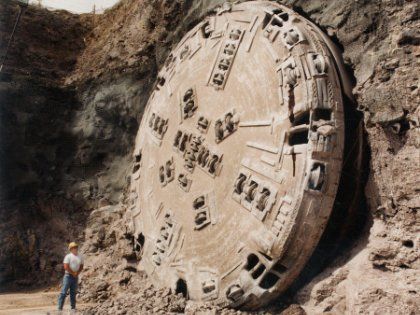
The Waste Isolation Pilot Plant, WIPP, was also the subject of political opposition, mostly at the state level. Locally it had a lot of support, perhaps largely because of the positive economic impact on the area. A notable opposition character was New Mexico Governor Bill Richardson. After much political wrangling and delays, the WIPP facility was opened with a formal ribbon-cutting ceremony featuring the new Secretary of Energy himself - Bill Richardson!
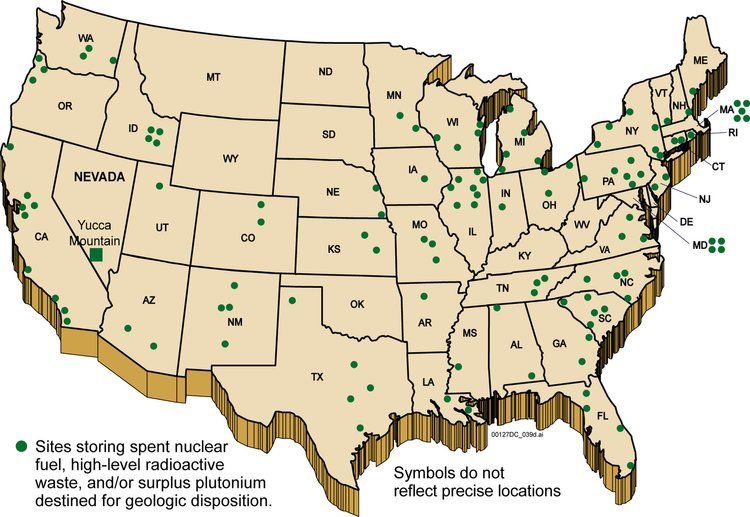
Waste in general, from municipal waste to nuclear waste, poses problems to manage. While we have thousands of storage and disposal sites all over the country for most types of waste, the volume of HLW and spent fuel nuclear waste compared to the other types is relatively minuscule. Emplacing it in a single, carefully managed facility would seem to me to be a much better alternative to leaving the material scattered around in numerous above-ground locations mostly managed by utility companies and not the government.
I’m not a geoscientist or a politician, but the Yucca Mountain concept seemed to be a good idea to me. Among the things that appealed to me was that the spent fuel would be accessible in the future. Although we currently do not reprocess nuclear fuel for re-use in reactors, that capability might be very important in the future if we build more reactors for power generation.
The issue of nuclear waste management is unfortunately similar to managing the COVID-19 pandemic. I’m a believer in vaccination and the science that backs it up but I know there are people that will never be convinced that the vaccines are a good idea. There is, I believe, a larger share of people who believe that nuclear waste can never be safely stored and I have little belief that I or anyone else could convince them otherwise. I wish I were more hopeful, but I’m pessimistic about that.
Thanks to Tom Kocialski for his generosity with his time and his patience explaining vitrification. Thanks as well to our wonderful Members who gave feedback on diagrams and to Nick for suggesting a new set of graphic design guidelines. If you’re looking for further reading, see BLDBLOG’s interview with DOE geoscientist Abraham Van Luik who worked on the Yucca Mountain repository, this report on the equipment design at West Valley, this short history of the HLW processing at the West Valley site, and this longer report about vitrification at West Valley.