Hey hey, happy Friday, we're basically there. I think I'm around 80% myself, mostly keeping up with things, just need to find a new home for the drill press that I lovingly restored a few years ago, plus catch up on tons of writing, find a few new jobsites to umarell at, and plan myself a couple long bike rides for the summer. Could be worse đ§
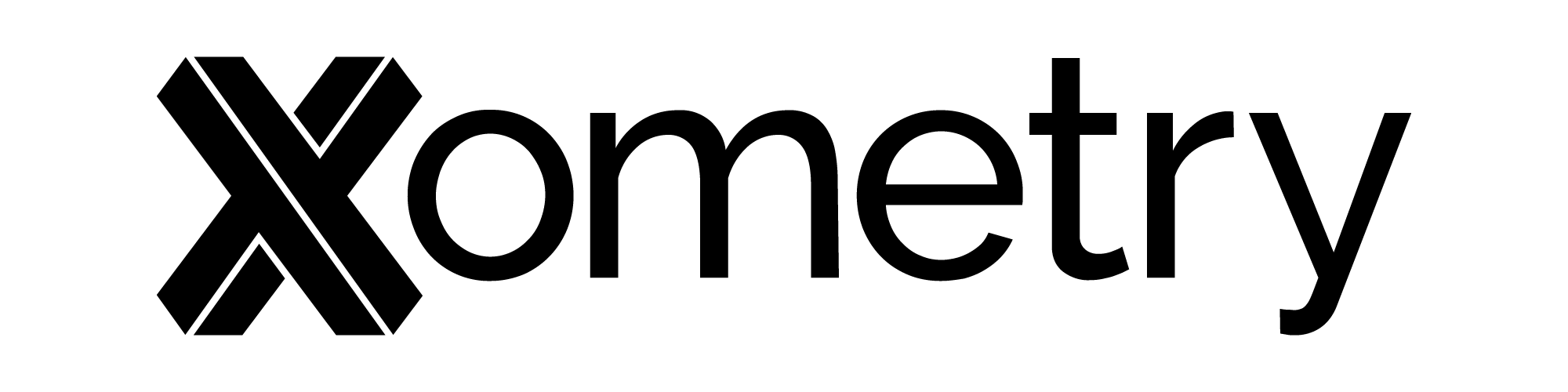
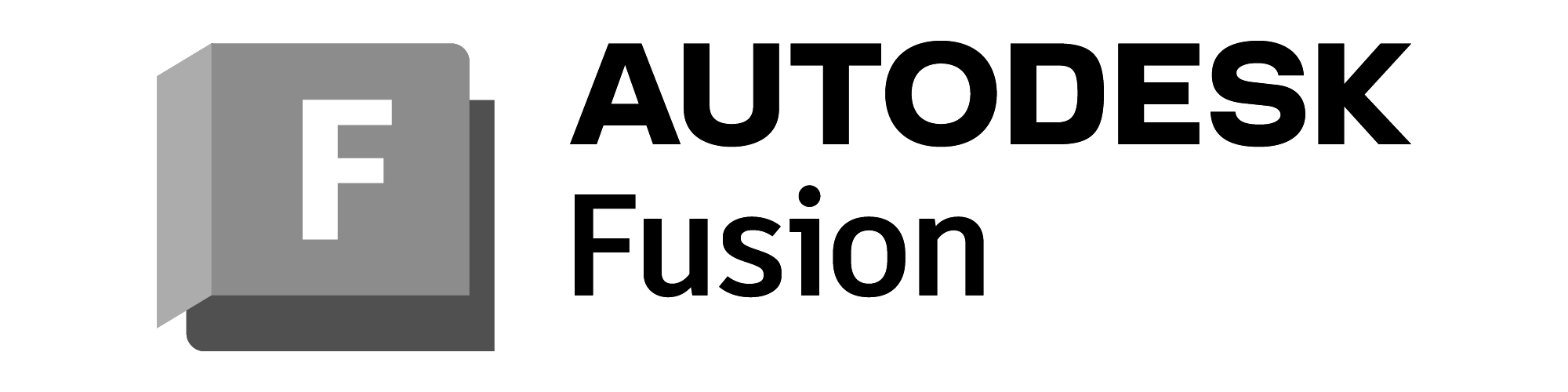
SCOPE CREEP.
- In case you missed it: SOW is holding a competition for umarelling, which gives you an excuse to pause on your way past a construction site, jot some notes down or make a quick sketch, and send them our way. I assure you that this is a relaxing and energizing activity, and that our judges are looking forward to your entries, and that notable entries may even get you published in this very newsletter ;)
- Hereâs a design patent, issued to Apple, for a glass staircase.
- Hereâs a utility patent, issued to one William O. Holmes, for a breathing tube that the user inserts into the bowl of a toilet, past the trap, so that they can breathe "fresh" air from the sewer vent. They do this â breathe sewer gas â because apparently the hotel theyâre staying in is on fire and the room is full of smoke.
- A short blog post on Kroil, the âworldâs best penetration oil.â One of the testimonials quoted includes reference to an Ideal Stencil Machine, which I was not previously familiar with. This website (which was created by a German type design studio) has a bunch of info on these machines, and this video shows an Ideal #3 (which produces text 7/16â tall) in operation.
If you worked in maintenance on a battleship â say, the Battleship New Jersey, which just so happens to be at a dry dock in Philadelphia right now, having some major work done â then you might get a lot of use out of an Ideal Stencil Machine (or an analogous machine made by Marsh, which is actually on board the Battleship New Jersey and is shown in this video). Think of it: Youâre enlisted. Youâre out at sea. You spend a lot of time doing basic maintenance, including painting. Lots of the stuff you paint has identifying or functional information painted onto it, and you need to replicate that information, so you cut lots of stencils, and you spray (or maybe dab) paint over the stencil to make whatever marking you need to replicate.
One of the things that happens when you paint, though, is that the paint is thicker in some areas than in others. This is probably fine for your battleship, but there are all kinds of things that you might want to apply a really consistent coating to. So you use physical vapor deposition, which is common on things like cutting tools (coated here with TiN, TiCN, and other really hard and colorful stuff), and snack packaging (in this 1993 academic paper by a Frito-Lay employee, vacuum metallized polyester is described as âindustry standardâ), and the artwork of Larry Bell.
Larry Bell is a sculptor who lives in Taos, New Mexico; he and his large, stainless steel vacuum tank were transplanted there from Venice Beach around 1975. As he describes in this well-shot and compelling mini-documentary, Bell got into vacuum metallizing in the 60s, after having spent a bunch of time messing with commercially-produced mirrors. At the time he had no mechanical experience, but with a combination of mentorship and a little bit of tough love from a decorative metallizer in the Bronx, Bell learned the trade himself. Bell says that he "doesn't want to play with" things that are overly exotic, but then again there he is, an eighty-something-year-old artist hopping into a big vacuum tank, metallizing glass and laminating thin films together. All of which strikes me as reasonably exotic, and I'm left wondering what kinds of obscure industrial processes I might take up, only to brush off casually as just something that I'm playing with.
...Very much unrelated to where this đended up, but semi-related to where it began: When I was attempting to build custom bicycle frames professionally, I inherited (from someone whose custom bicycle frame business had failed, as mine eventually did) a New Hermes Engravograph. The machine, which combines a pantograph and an engraving cutter, was a real old school way to cut letters into metal, and it was pretty early-2000s of me to think it would play a meaningful role in my business. Anyway, hereâs a video of someone using a New Hermes Engravograph to make a tag for their hydraulic press.
Two additional notes here:- The company which made Bell's vacuum tank, Edwards Vacuum, has a short series of vacuum experiments on their YouTube page. While some of these do require a vacuum pump, they're all reasonably accessible, and I could see doing at least one or two of them with my seven-year-old.
- Here's a pretty good explainer video about a pretty impressive DIY physical vapor deposition setup.
- I very much enjoyed this, from Computing Taste (which the SOW Members' Reading Group is almost done with):
In the winter of 1857 [polymath Hermann von] Helmholtz presented a lecture in Bonn, âThe Physiological Causes of Harmony in Music.â In his lecture, which touched on the connections between music, physics, and the anatomy of the ear, he gave an unusual description of a concert: âFrom the mouths of the male singers proceed waves of six to twelve feet in length; from the lips of the female singers dart shorter waves, from eighteen to thirty-six inches long. The rustling of silken skirts excites little curls in the air, each instrument in the orchestra emits its peculiar waves, and all these systems expand spherically from their respective centers, dart through one another, are reflected from the walls of the room and thus rush backwards and forwards, until they succumb to the greater force of newly generated tones.â In Helmholtzâs account, the world is awash in vibration and resonance; it is âa variegated crowd of intersecting wave systems.â Not only music, but the whole audible world is full of repeating waves, everywhere⌠the world is overwhelming and filtering is a basic precondition for acting within it.
Thanks as always to Scope of Workâs Members and Supporters for making this newsletter possible. Thanks also to Joe and Xavier for helping source links this week.
Love, Spencer.